Register now for our Additive Manufacturing Advantage online event for insights on AM developments in aerospace, space, and defense sectors from industry leaders!
Materials technology company Diamond Hard Surfaces has partnered with the University of Wolverhampton’s AM research spinout, Additive Analytics, to investigate the development of embedded electronic heat spreaders aimed at enhancing performance.
Akin to heat sink geometries, these components are critical for managing thermal dissipation in electronics and CPUs. Traditional subtractive manufacturing techniques have historically limited the complexity of heat spreader designs. The project emphasizes the use of 3D printing technologies to fabricate heat spreaders with complex geometries and enhanced material properties, promising better heat dissipation efficiency compared to conventional manufacturing approaches.
Chris H Walker, CEO at Diamond Hard Surfaces, said, “We are very excited to have the opportunity to work with the University of Wolverhampton and Additive Analytics; two of the leading players worldwide in the field of additive manufacturing using copper-based materials. We are hoping this will lead to a number of new and innovative products and services which will benefit both our existing and new customers for thermal management devices.”
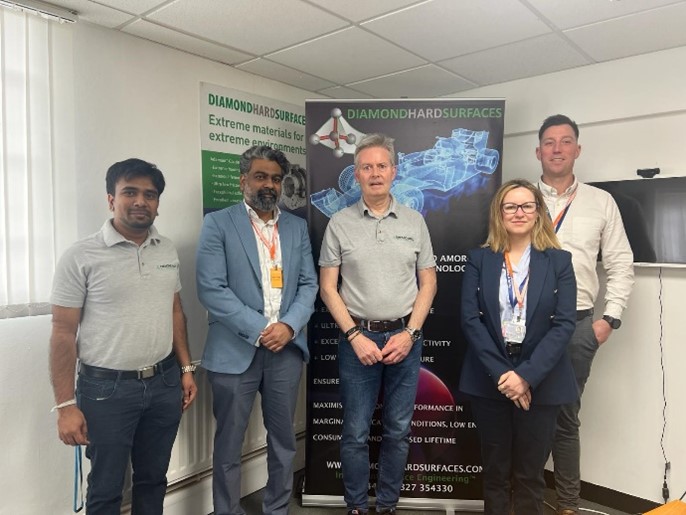
Optimized heat spreaders for electronics
Heat spreaders are essential for managing heat in electronic devices by distributing it evenly, preventing hot spots, and maintaining optimal temperatures to enhance performance and reliability. They mitigate thermal damage, prolong device lifespan, and improve energy efficiency by reducing cooling system workload.
Additionally, heat spreaders facilitate compact device designs without sacrificing thermal management capabilities, making them crucial in consumer electronics and industrial applications alike. Overall, these components play a critical role in ensuring efficient thermal dissipation, thereby supporting the long-term functionality and durability of electronic systems across various sectors.
For this project, Diamond Hard Surfaces’ patented processes and industry-specific knowledge are integrated with Additive Analytics’ data-driven material development and laser processing techniques, says the company.
By adopting this method, heat spreaders can be developed to maximize surface area-to-volume ratios, thereby improving heat exchange efficiency. Such developments are especially valuable in the electronics, automotive, and aerospace sectors, where maintaining operational reliability and performance hinges on effective thermal management.
Elsewhere, the University of Wolverhampton partnered with 3D printer manufacturers EOS and AMCM to establish the UK Center of Excellence for Additive Manufacturing. Located at the Elite Centre for Manufacturing Skills on the Springfield Campus, the center focuses on advancing copper 3D printing for sectors including aerospace, automotive, electronics, and quantum computing.
It aims to integrate laser process data with AI to enhance printing efficiency and has received partial funding from the UK’s Regional Innovation Fund (RIF). The initiative was launched during MACH 2024, highlighting a commitment to innovation and sustainable manufacturing.
Thermal management for electronics
Thermal management in electronics is crucial for maintaining reliability, performance, and safety. It ensures components operate within optimal temperatures, reducing the risk of overheating-induced failures and extending the device lifespan. Efficient thermal management also supports consistent performance by preventing thermal throttling and enhancing energy efficiency.
In line with this, RMIT University researchers developed a novel type of 3D printed heat exchanger designed for use with jet fuel as a coolant. Referred to as “3D printed catalysts,” these heat exchangers were created by coating metal structures with synthetic minerals known as zeolites. According to the researchers, this innovation has the potential to solve a significant obstacle in hypersonic flight: excessive heat buildup.
Another example includes a collaborative effort between GE Research, the University of Maryland, and Oak Ridge National Laboratory (ORNL) resulted in the successful testing of a 3D printed heat exchanger prototype. This subscale thermal regulation device, designed with a unique grape-like geometry, withstood temperatures exceeding 900°C. This achievement signifies a potential improvement in heat exchanger technology.
Join the Expert Committee for the 2024 3D Printing Industry Awards to help select the winners!
What 3D printing trends do the industry leaders anticipate this year?
What does the Future of 3D printing hold for the next 10 years?
To stay up to date with the latest 3D printing news, don’t forget to subscribe to the 3D Printing Industry newsletter or follow us on Twitter, or like our page on Facebook.
While you’re here, why not subscribe to our Youtube channel? Featuring discussion, debriefs, video shorts, and webinar replays.
Featured image shows the Additive Analytics and Diamond Hard Surfaces team. Photo via University of Wolverhampton.