Netherlands-based independent 3D printing resin manufacturer Liqcreate has shared valuable insights into its Wax Castable resin’s versatility and wide-ranging applications, which has become a popular choice in various casting industries.
According to the company, the casting industry was one of the earliest to integrate 3D printing technology into its processes, largely due to the high level of detail and complex organic shapes that resin 3D printing can produce.
Introduced in 2020, Liqcreate’s Wax Castable resin serves multiple industries by being compatible with MSLA, DLP, and laser-based systems. The resin offers high processability and accuracy, capturing intricate features and crisp details. Its wax-based formula ensures smooth surfaces, making it ideal for jewelry, dental, and industrial applications.
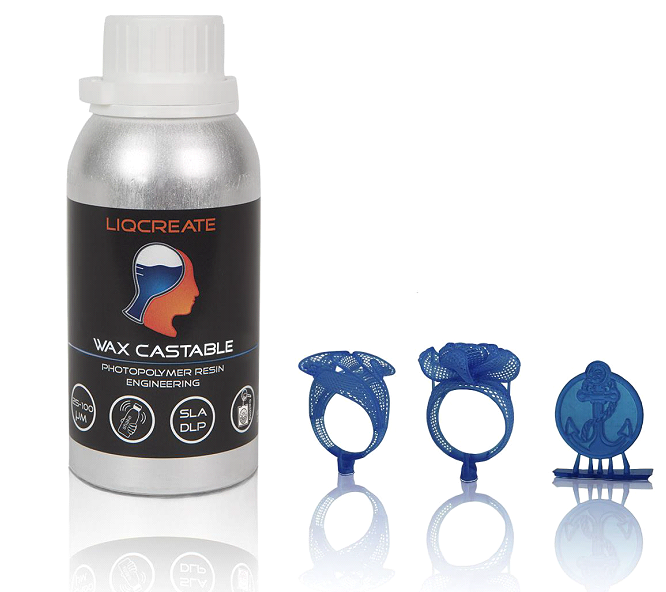
Achieving detailed casts with the Wax Castable resin
One of the key applications of Liqcreate’s Wax Castable resin is in the jewelry industry. Professional caster Mr. Dombrun, a longtime partner of Liqcreate, conducted extensive tests with the resin to determine its performance in quick burn-out cycles for casting jewelry in materials such as Brass and Bronze.
He found that the resin worked exceptionally well, allowing for intricate designs and detailed engravings to be faithfully replicated in the final metal pieces. Through his tests, Mr. Dombrun discovered that factors such as cylinder placement in the oven and gradually increasing the temperature were crucial to achieving optimal casting results.
These careful adjustments ensured that the combustion gases from the wax-based resin could escape properly, leading to a smooth and successful casting process.
Liqcreate’s Wax Castable resin has proven effective in casting various metal alloys. Mr. Denny, from the YouTube channel “Shake the Future,” has been experimenting with various metal alloys and casting methods.
Using a casting oven he built himself, he successfully cast jewelry using Copper, Aluminum, and Brass. By carefully managing the thermal burn-out process and selecting the appropriate investment material, he is able to work with a wide range of metals.
In addition to its use in jewelry, Liqcreate’s Wax Castable resin has also found a home in the sculpture casting industry. ANAfoundry, a company specializing in bronze art and casting, has integrated resin 3D printing into its workflow, transitioning from traditional hand-sculpted wax and filament-based 3D printing to resin-based methods. While filament-based 3D printing provided some benefits, it lacked the level of detail necessary for high-quality bronze casting.
The switch to resin printing, particularly with Liqcreate’s Wax Castable, enabled ANAfoundry to produce more accurate sculptures and fewer casting defects. ANAfoundry tested various resins, from budget-friendly to premium options, often encountering resin residue issues when casting statues.
However, this was not a problem with Liqcreate Wax Castable due to its wax-based formula. While some other wax-based resins gave similar results, they were significantly more expensive—up to four times the price of Wax Castable. For best results, printing with Wax Castable should be done at 20°C (68°F) to 25°C (77°F), as the lower temperature can cause solidification of the wax. If the resin solidifies, Liqcreate has advised to gently heat the resin above 20°C to liquify it again.
Additionally, jewelry company Stevens Sieraden has crafted another exceptional piece using a blend of traditional craftsmanship and 3D printing technology. The 18-carat gold ring was designed and 3D printed using Liqcreate Wax Castable resin, then cast in gold. Afterward, the Chrysoprase stone, cut by Stevens Sieraden, was set alongside sapphires arranged around it. Discover more of their creations featuring Liqcreate resin and gold or silver casting here.
Expanding applications in dentistry and beyond
Liqcreate’s Wax Castable resin also plays a role in dental applications, particularly in the creation of removable partial dentures (RPDs). RPDs are designed for patients who require partial tooth replacements but cannot have fixed dentures.
Using Liqcreate Wax Castable, dental professionals can design and print RPDs, which are then cast in metal using materials like ChromeCobalt. This process provides an efficient and cost-effective solution for creating custom dental appliances.
The versatility of Liqcreate’s Wax Castable resin also extends to semi-professional users and beginners. Vlogger Vogman demonstrated that even with minimal experience, users can achieve successful casting results using this resin.
In his instructional video, Vogman outlines the steps involved in printing and casting with Liqcreate Wax Castable, providing helpful tips on how to handle the material effectively. This ease of use makes the resin accessible to a wider range of users, from hobbyists to small business owners.
Custom resin development and OEM
For customers with specialized requirements, Liqcreate offers customized resin development services. As part of this service, users can request specific modifications to the resin’s properties, including its print speed, color, wax content, and mechanical characteristics.
This customization ensures that the resin is well-suited to the user’s platform and application. Liqcreate’s in-house capabilities in research and development (R&D), sales, and manufacturing allow for rapid production scaling, making it an ideal partner for 3D printing bureaus and manufacturers, says the company.
Customers interested in Liqcreate’s material portfolio, including the Wax Castable 3D printing resin, can visit the Liqcreate website or contact a Liqcreate representative or dealer for more information and order details.
Nominations for the 2024 3D Printing Industry Awards are now open. Cast your vote today!
What 3D printing trends do the industry leaders anticipate this year?
What does the Future of 3D printing hold for the next 10 years?
To stay up to date with the latest 3D printing news, don’t forget to subscribe to the 3D Printing Industry newsletter or follow us on Twitter, or like our page on Facebook.
While you’re here, why not subscribe to our Youtube channel? Featuring discussion, debriefs, video shorts, and webinar replays.
Featured image shows Liqcreate’s Wax Castable resin. Image via Liqcreate.